KPIs
Using KPIs to stay on track
Key Performance Indicators (KPIs) are critical metrics used by companies across various industries to gauge their performance and success. In the construction industry, where projects are complex and multifaceted, the use of KPIs can be particularly beneficial. These metrics provide valuable insights that can lead to improved decision-making, enhanced productivity, and increased profitability.
Enhanced decision-making
One of the foremost benefits of using KPIs in a construction company is the enhancement of decision-making processes. By accessing quantifiable data, Donley’s can make informed choices based on objective insights rather than subjective opinions. Whether it's turnover rates, resource allocation, or determining financial health of a project, this data offers a clear and concise representation of current performance. This clarity enables our leaders to identify potential issues early and take corrective actions promptly.
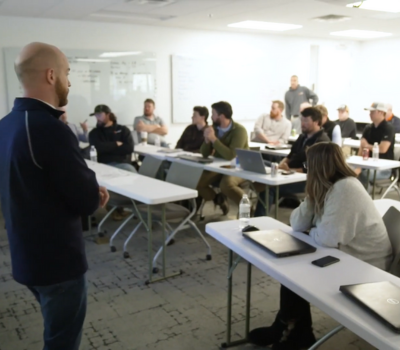
Increased productivity and efficiency
KPIs enable construction companies to identify and eliminate inefficiencies in their processes. For example, tracking labor productivity KPIs can highlight areas where workforce performance can be improved. Similarly, equipment utilization data can reveal underused machinery, leading to better resource management. By addressing these inefficiencies, companies can enhance overall productivity and reduce waste, resulting in cost savings and improved project outcomes.
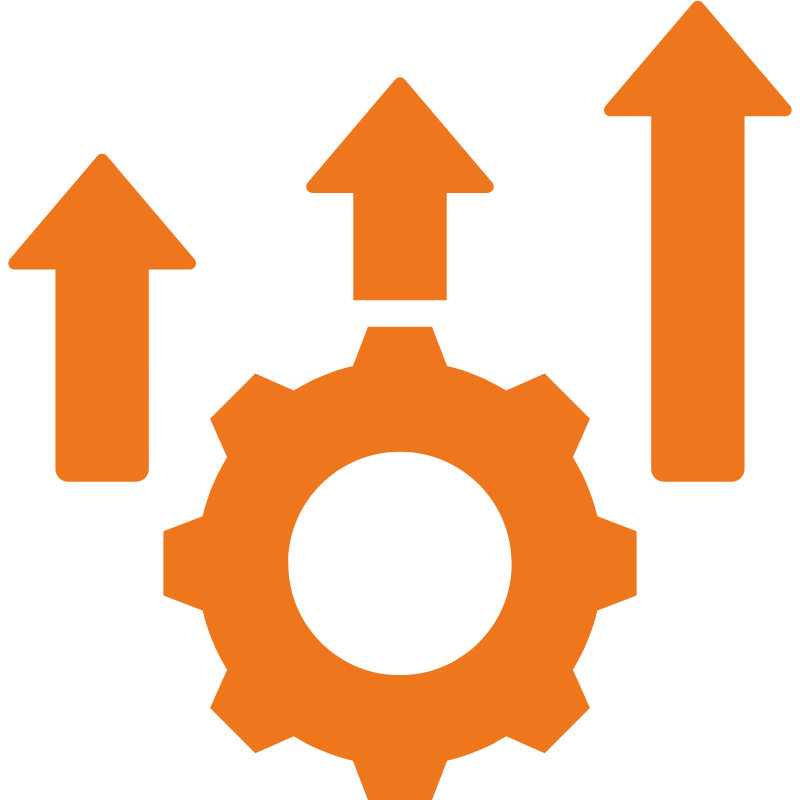
Better risk management
KPIs facilitate better risk management by providing early warning signals of potential issues. For instance, safety KPIs such as the number of incidents or near-misses can help in identifying unsafe practices and implementing preventive measures.
Financial key performance indicators like cash flow and profit margins can reveal economic risks, allowing us to take proactive steps to mitigate them. By continuously monitoring these indicators, Donley’s minimizes risks and enhances project stability for our clients.
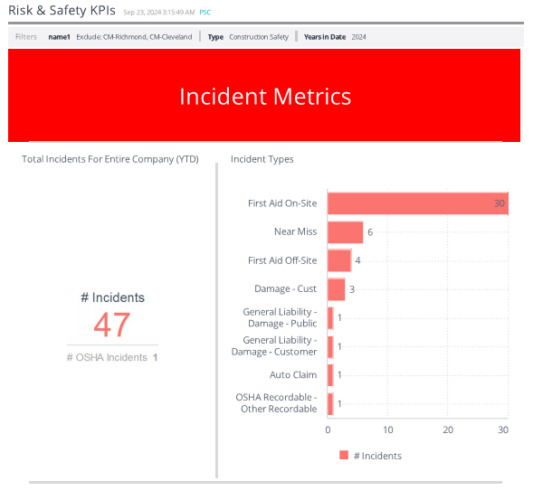
Enhanced client satisfaction
KPIs enable construction companies to identify and eliminate inefficiencies in their processes. For example, tracking labor productivity KPIs can highlight areas where workforce performance can be improved. Similarly, equipment utilization key performance indicators can reveal underused machinery, leading to better resource management. By addressing these inefficiencies, companies can enhance overall productivity and reduce waste, resulting in cost savings and improved project outcomes.
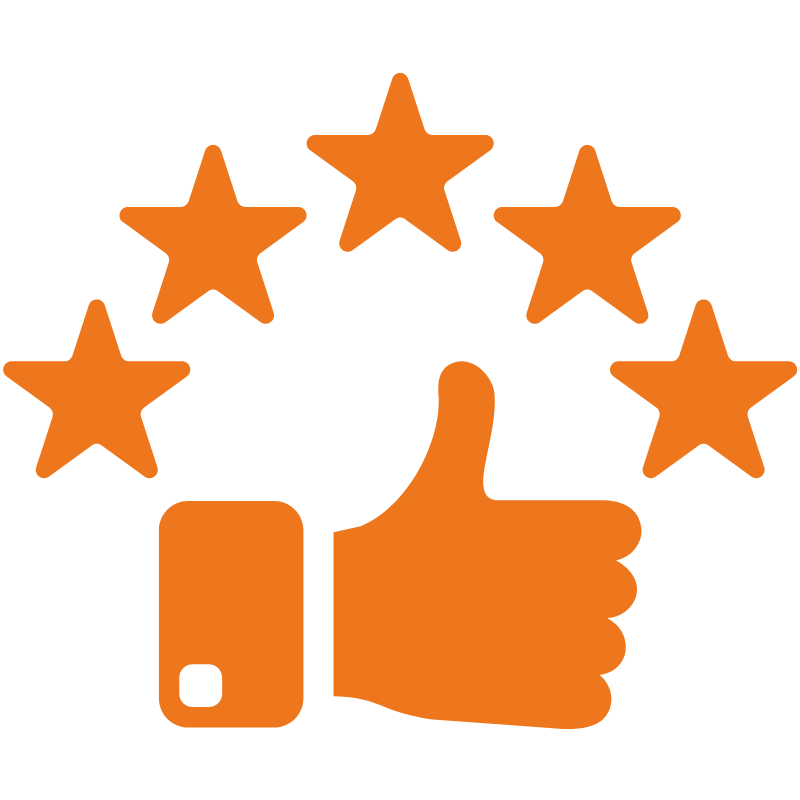
Benchmarking and continuous improvement
KPIs provide a framework for benchmarking our performance against industry standards and competitors. This comparative analysis enables us to identify areas where we might lag and implement strategies for improvement. Moreover, these metrics foster a culture of continuous improvement by encouraging regular performance reviews and adjustments. By striving for continuous enhancement, Donley’s stays competitive, enabling long-term success.
Valuable insights
KPIs provide valuable insights that drive success. The integration of them into Donley’s business has without a doubt enhanced our decision-making. In addition, by fostering a culture of continuous improvement and accountability, we achieve higher levels of performance and client satisfaction.
What gets measured gets done.
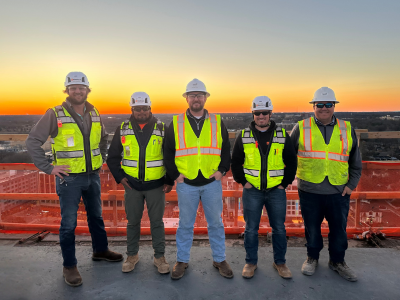