5S
Sustaining excellence
The 5S methodology is a systematic approach for organizing and maintaining a safe and productive workspace. Originating from Japan and deeply rooted in the manufacturing sector, it has since been widely adopted across various industries for its effectiveness in improving operational efficiency and fostering a culture of continuous improvement.
5S: What it is and what it means
On the jobsite, following 5S principles builds a quality work environment. Our team members find it more enjoyable when the workplace is safe, clean, uncluttered, and free of waste. Other benefits include increased customer confidence, better reputation, improved safety, and higher quality. Below is a summary of the 5S principles and examples of Donley’s application:
1. Sort
This principle emphasizes the importance of decluttering and eliminating anything that does not contribute to productivity or is not required for current operations. By doing so, it helps to free up space, reduce distractions, and improve workflow. The key question to ask during this stage is: "Do we really need this item?"
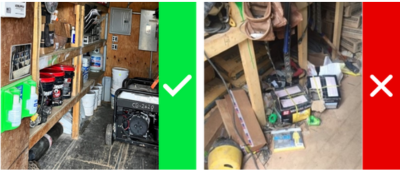
2. Set in Order
Once unnecessary items have been removed, the remaining ones should be organized in a way that makes them easily accessible and quickly retrievable. This could involve labeling, creating designated storage areas, or employing visual controls. The aim is to ensure that everything has a specific place and can be found without wasted time or effort.
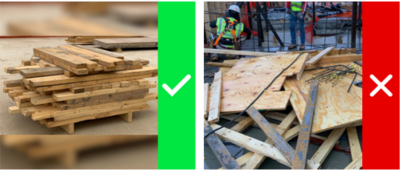
3. Shine
This principle is not just about cleanliness but also about identifying and addressing potential issues before they escalate. Regular cleaning routines help to maintain equipment, prevent defects, and ensure a safe working environment. Perhaps most importantly, this creates a sense of ownership among employees, encouraging them to take pride in their workspace.
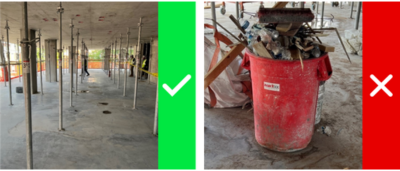
4. Standardize
This involves creating consistent procedures and guidelines to ensure that the benefits of the first three S’s are maintained over time. The goal is to make the processes repeatable and scalable, reducing variability and enhancing predictability.
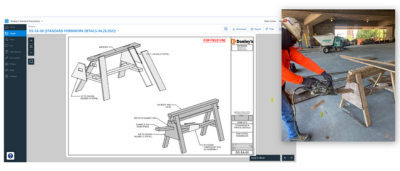
5. Sustain
The final principle emphasizes the importance of sustaining the 5S practices through discipline and continuous improvement. This requires fostering a culture where adherence to the 5S principles becomes a natural part of everyday operations. Regular audits, training, and involvement of all employees are crucial for sustaining the progress made. The aim is to embed the 5S mindset into the organizational culture, ensuring long-term success.
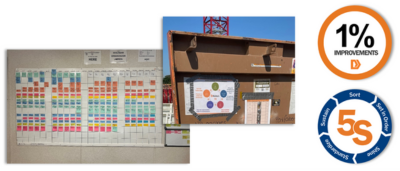
Creating an enjoyable work environment
Donley’s leverages the 5S methodology as a practical and effective framework for enhancing workplace efficiency and organization. By systematically implementing these principles, we create a more productive, safer, and enjoyable working environment. The 5S approach not only improves physical conditions but also fosters a culture of continuous improvement and employee engagement, laying the foundation for our sustained operational excellence.